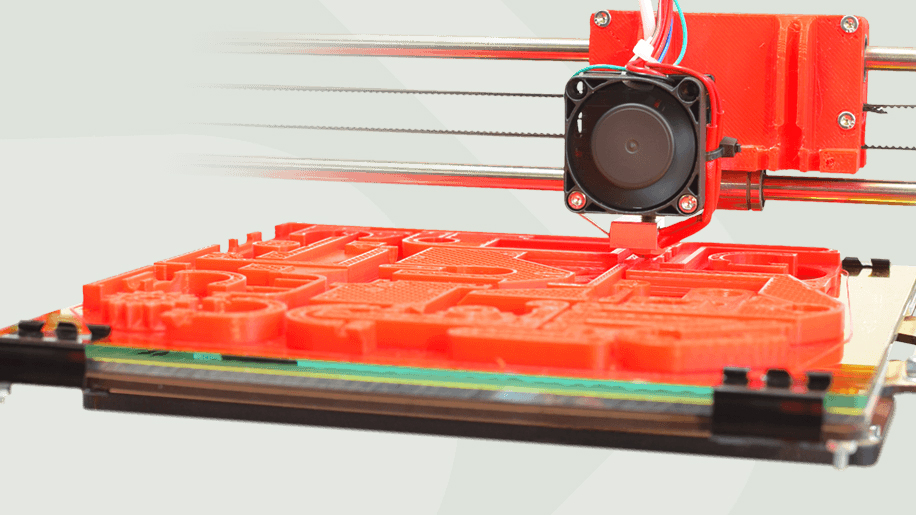
We don't how many RepRap 3D printers are in existence, and that's because everyone who owns a RepRap can use it to make another - and another, and another. The RepRap's creator, Adrian Bowyer, designed it to be self-replicating. We sat down with him to talk about the international community of enthusiasts that brought RepRap to fruition, and how open-source hardware can help propel a low-cost design to popularity and world domination.
TechRadar: How did RepRap start?
Adrian Bowyer: I've always been interested in the idea of an artificial, self-replicating machine. As a child, it seemed obvious to me that human beings don't make things in the right way.
Plants make things in the most efficient way. The plant is a self-replicating object, entirely composed of self-replicating cells. So if you want to make things, you start with things that can make themselves. That's the basis of what was going on in my mind.
I bought a couple of 3D printers. They were big commercial machines - the only type available then - and the cheapest one was worth £250,000. We started using them, and found them to be a very useful resource.
As an engineer, it was complete liberation. I could just think of something, design it and have it in my hand. It also occurred to me that we had a technology that was versatile enough to replicate itself. That's where the idea "we'll make a 3D printer that prints itself" came from.
I realised we had to make this open source. This is because if you have a self-replicating machine and try to close it off and copyright it, you're basically saying you're trying to stop the one thing that you designed the machine to do.
Sign up for breaking news, reviews, opinion, top tech deals, and more.
TR: How long was it from the initial start to having a working printer?
AB: Work actually started in 2005 and we had our first functioning machine two years later in 2007. A year later, that machine had printed a complete set of parts to make a copy of itself.
Obviously, there were tweaks and changes along the way. We made the very first copy in May 2008. Therefore, by that point we'd reached a partially self-replicating printer.
We never thought from the beginning it would be able to print 100% of itself. The idea was to print all the fiddly pieces and make sure all the other bits required to make the machine were widely available. It's about 50/50 - 50% printed parts and 50% bought parts. We've got the specialist parts down to just one or two.
TR: What was the first thing that you printed?
AB: One of the very first things we printed was a coat hook. An economist once told me that the world market for coat hooks is bigger than that of jet engines. When you think about it, it isn't that surprising - it's just you never think of coat hooks as being major engineering products in the same way as jet engines.
TR: And that model could be uploaded?
AB: We did upload it, so anyone who wants to print that part can. The whole law of intellectual property is quite interesting. If you're Ford or whoever, you can't patent a bonnet latch like an idea.
You can patent the design, but that just stops people copying the computer files - they can't stop you copying the object. You can't copyright a 3D object unless it's a sculpture.
TR: Do you see this causing changes in the law further down the line?
AB: That's difficult to say - how would it be policed? We have copyright for music and it's effectively ignored by millions of human beings. So if you try and pass a law that makes what everyone does in the privacy of their own home an offence, it's never going to work.