I built my own audiophile headphones at Sennheiser's factory, and saw how elite sound tech comes together
I visited Sennheiser's facility in Ireland to see how the audio sausage is made, and it's possible that you could too
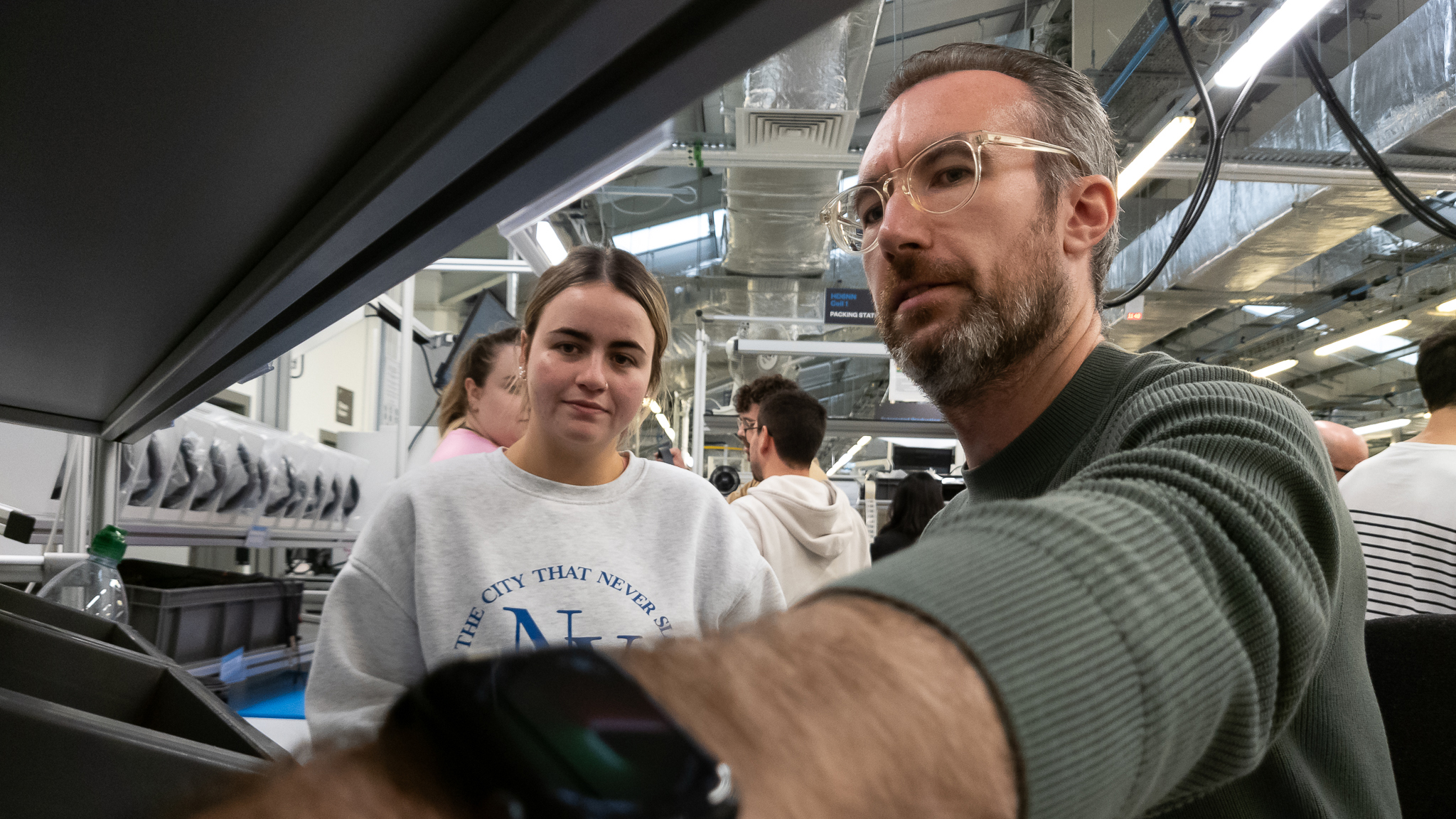
In late 2023, I was offered the chance to visit Sennheiser's factory in Tullamore, Ireland, to find out how it builds the different headphones that come from this factory – including the ultra-elite Sennheiser HE-1 headphones and amp package – and to have the chance to build a pair of the best wired headphones for myself.
I was in a group with other audio journalists, but the experience I had will actually be offered to "members of the audiophile community", with exclusive invitations handed out in 'Golden Tickets'. Information on opportunities to get one will come through Sennheiser's social media and Reddit – it's not like anyone can just book to rock up to the factory, but it could be possible for you to make the same visit.
We started with a tour of the automated part of Sennheiser's headphones manufacturing, and we mostly focused on how the transducers are built. These are what you find inside the earcup, with the speaker driver and the electronics to support it.
Sennheiser explained how it balances creating specialized part with efficiency, using sets of machines in "cells", where a group of manufacturing machines are all connected into a single production line focused on making a particular part, which can then be moved to another area for assembly into the actual headphones.
The trick is that, despite the precision involved, these machines are not limited to making only one kind of transducer. They can do a run of transducers for the Sennheiser HD-660S2, for example, with the particular connections and setup for those headphones, ready for assembly later. Then it can be switched to making a different 38mm transducer spec for a different pair of headphones, which is running while the Sennheiser HD-660S2 transducers are being assembled into finished headphones.
The manufacturing cell basically takes things start to finish on the transducers; you can watch mesmerizing machines spin magnetic coils from ultra-fine metal threads, add the various parts over time, seal them with heat, and more – leading up to testing as part of the production process. Each transducer's accuracy is tested as soon as it's been made, with a readout showing whether its capabilities are within acceptable margins, and what the current failure rate on the cell is. These machines are usually nearly 100% successful anyway, but if there's an unusual number of failures, it can be caught rapidly and engineers can step in to see what's up.
This isn't the part of building headphones that I experienced, unsurprisingly (though Sennheiser says that some transducers are made by hand still, because their designs don't lend themselves to being made by machine, though didn't clarify much on what this meant in practice). The tour given by Sennheiser's experts was fascinating, pointing out all the little intricacies of the process, and where to look for the most interesting machine work. Sadly, I couldn't take pictures of my own within the factory to point this out to you (the pictures on this page of us on the factory floor were provided by Sennheiser).
Sign up for breaking news, reviews, opinion, top tech deals, and more.
But one of the most impactful moments about the precision of the components came away from the machines, when I was handed the coil used in the Sennheiser HD-800 headphones, before it's then built into the rest of the transducer.
The two ends of the metal thread dangle loose at this stage, and I held it by grabbing these two threads… and they were so thin that I literally could not feel them between my fingers. I couldn't differentiate them by touch from the grooves in my skin; the only way I knew I was holding something was because I could see it. It was surreal, and such an impactful demonstration of what goes into this tech.
The actual assembly is done in cells, too, to add to the flexibility of the factory. There are different areas for putting together different models of headphones, where the transducers, headbands earbuds and padding are all combined. Not all headphones are being made at any one time – teams (who always work together, and rotate through jobs within a cell) move from model to model, depending on what's needed and when.
This is where I got to try my hand at building the headphones. We were introduced to the team who were building Sennheiser HD-600 models that day, which involves assembling the final unit, testing the quality of the headphones, and then boxing them up to go out to customers.
This particular model comes in a few separate parts. The electronics side has come from the manufacturing cell I described above, all in one complete unit per earcup. The headband, earcup and ear padding are the other separate pieces that will go into making the final headphone.
First, I needed to place the transducer unit in the earcup, then I needed to cover the driver with a mesh layer, and then attach the padding, sealing it all together. There's a trick to securely attaching the padding; quite a few of our group failed this part a few times. It needs to click firmly into a locking system in the earcup, but it's not easy to press hard on something that's squidgy. One of the team showed me her trick of digging her thumbs in and pushing slightly out, and I was able to get a good seal all the way around. Experience is where it's at.
Then we needed to attach the earcups to the headband, which is done at the hinges where the earcups can flex to fit the shape of your head. These connect on each side of the earcup, and they also need to be inserted with a firm hand. At first we were all too scared of damaging something, but the team who works on the assembly showed us that we really didn't need to treat them delicately – which was also reassuring as to the general toughness of these headphones, in a way that's hard to know from any other context.
Next, they went into a booth for final testing. The headphones were placed on a stand with microphones in, and connected to cables – the correct ears have to go on the correct side, of course. Amusingly, they go on this stand backwards, so the left earcup is on the right. I asked as many people as I could find if that was for some interesting technical reason or just how it ended up being built… no one was entirely sure. One of those technical mysteries we all have in our workplace.
A mistake in the construction can mean that the sound output is affected, or perhaps a transducer gets damaged once it's left the manufacturing machine, so this test is vital. The equipment is sensitive enough that it can be affected by speaking outside of the booth, so a failure doesn't mean the headphones definitely need to be scrapped – retesting can make it clear that it's an environment problem, not a device problem.
My headphones passed the test first time; perfectly constructed. So now we moved on to boxing them up. Usually, someone has been building boxes for a while, so there's a stack ready to go. Headphones are placed in plastic bags, cables are packed in, labels go on the outside, and that's that.
I needed to make my own box, though, naturally. This was easily the most daunting part, because this elaborate flat shape is full of folds. Again, the team showed me the tricks of making it easy and fast, but unlike the part that just required me to go gung-ho with more force, this needed memory. I got it right with guidance, but while I think I could still put together the actual headphones correctly much later, I could not tell you where to start with the box.
Separate to all of this is a room at the side of the Tullamore factore. Only one man works in this section, sealed off from the rest in his own fishtank. This is where the $59,000 Sennheiser HE-1 headphones and valve amp are built, at a rate of about one a week.
Some of the parts for the HE-1 can be constructed in Ireland, some are too specialized even for this factory, and need to be sent from Sennheiser's facilities in Germany – the valve amps, for example, require a clean room for production that's not available here, so they're shipped over, but are still produced in-house. The marble enclosure is not carved here either, funnily enough.
As we finished our tour of the factory, we were led into a room next to the HE-1 manufacturing space, and in here is a listening room with an HE-1 unit, along with two pairs of HE-1 headphones (driven from the one amp). There's a turntable and a CD player, each with identical album options so you can compare the two. There's also a wall full of Sennheiser's headphones range, so you can also compare what the HE-1 can do to other (extremely good) headphones, and sample headphones that few people in the world will have the chance to try.
The HE-1 are clearly something special from the moment you turn them on and the hidden valve amps rise up out of the body, and a lid automatically lifts to reveal the headphones. It feels like it's from the future and the past at the same time.
The large, comfortable headphones slip on, the electrostatic drivers kick into gear with some vinyl, and you're treated to a level of sound depth and detail that swallows you whole. I'm not going to wax lyrical about the HE-1 here; I just hope that if you have the inclination and the chance at a hi-fi show or when it does occasional demo days at stores, you take it.
At the end of the tour, I was presented with a pair of Sennheiser HD-600, from the batch that I helped put together. Did I build this exact pair I'm holding? Who knows – I've been telling people I know that I did, because it's a cooler story. They'll be shocked by my white lie if they read this. But I don't actually know for sure – if you've bought a pair recently, maybe they're yours. That feels pretty cool to me, too.
You might also like
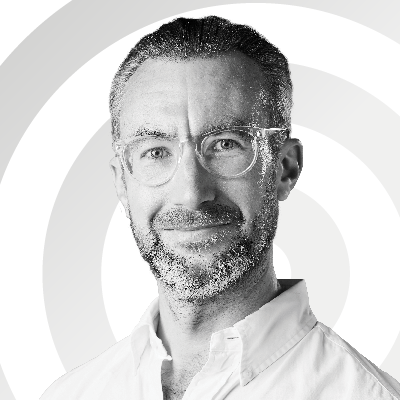
Matt is TechRadar's Managing Editor for Entertainment, meaning he's in charge of persuading our team of writers and reviewers to watch the latest TV shows and movies on gorgeous TVs and listen to fantastic speakers and headphones. It's a tough task, as you can imagine. Matt has over a decade of experience in tech publishing, and previously ran the TV & audio coverage for our colleagues at T3.com, and before that he edited T3 magazine. During his career, he's also contributed to places as varied as Creative Bloq, PC Gamer, PetsRadar, MacLife, and Edge. TV and movie nerdism is his speciality, and he goes to the cinema three times a week. He's always happy to explain the virtues of Dolby Vision over a drink, but he might need to use props, like he's explaining the offside rule.