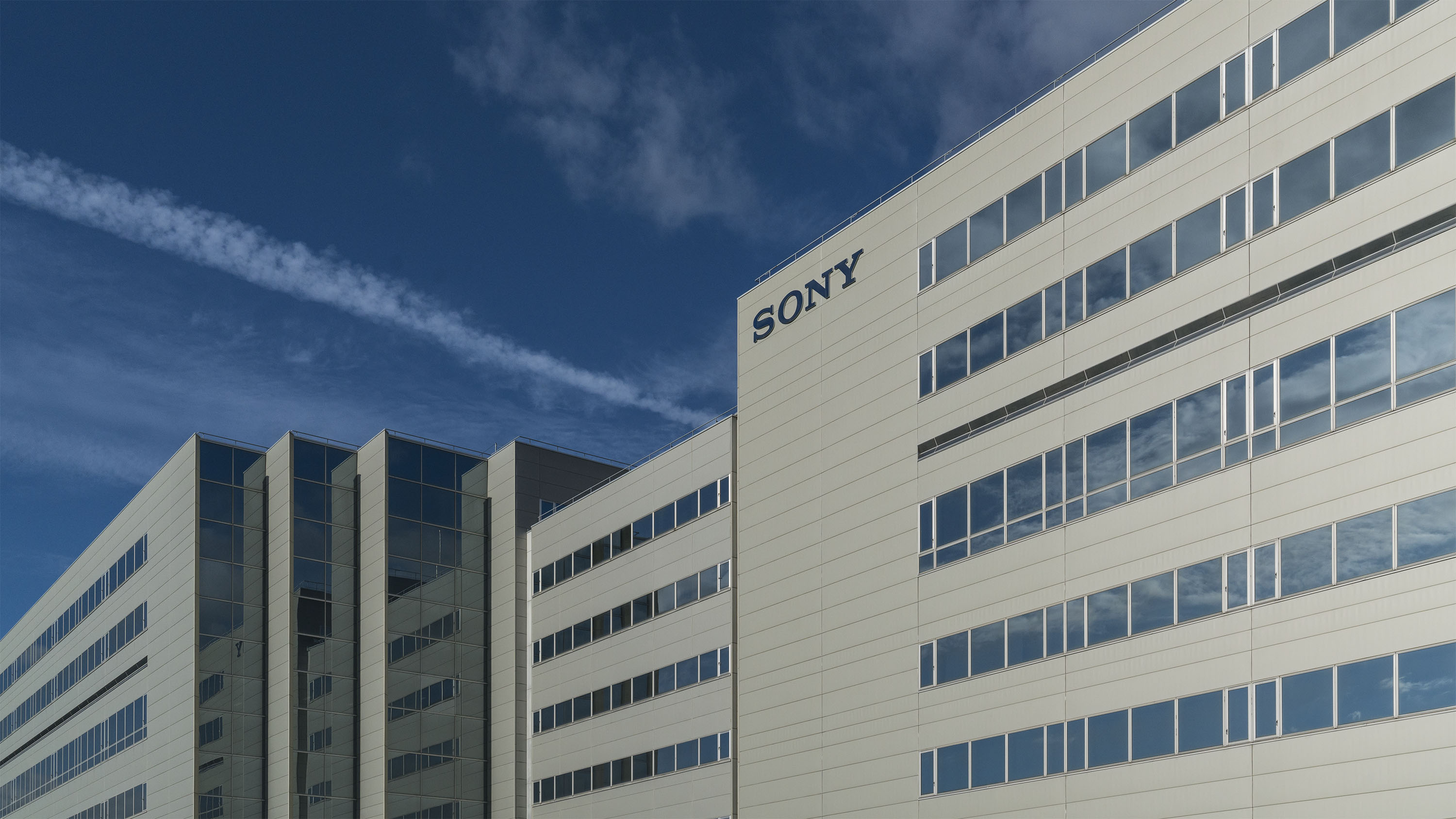
Whether your go-to camera is your smartphone or a full-frame DSLR, the chances are its sensor was manufactured in the sleepy prefecture of Kumamoto, which sits on Japan’s southern-most main island of Kyushu.
Some 550 miles from Tokyo, Kumamoto seems an odd place to set up a manufacturing hub for sensors, especially when you consider the relatively poor transport links. However, it’s the abundance of incredibly pure water here – its quality would make Evian blush – that's the key, as it’s essential in the production of image sensors.
It's why pretty much every semiconductor manufacturer has set up shop here, and TechRadar was invited to take a very exclusive look behind the scenes of Sony’s vast Kumamoto Technology Center.
A staggering four million sensors a day are produced for a wide range of imaging products
Home to the Sony Semiconductor Manufacturing Corporation, the Center produces a staggering four million sensors a day for a wide range of imaging products. Many will find their way into Sony-badged cameras and smartphones like the Alpha A7R III, Cyber-shot RX10 IV and Xperia XZ1, while others are destined for a host of cameras and devices from other brands that rely on Sony for their sensors.
The site is huge and is made up of two vast buildings, each six stories high, with most of the floors designed to support what are known as the massive 'cleanrooms' of the two buildings.
These are exactly what their name suggests: ultra-clean rooms in which external contaminants are kept to an absolute minimum. Before they enter, technicians have to put on fairly stuffy and claustrophobic all-over body suits, before having an air shower to reduce any particle contamination.
Not that we saw many people – for such a large site, the place was eerily quiet. That’s because pretty much the entire sensor production line is automated, with large box-sized carriers known as FOUPs ferrying their precious cargo of sensor wafers between each stage of the automated process.
Sign up for breaking news, reviews, opinion, top tech deals, and more.
It’s not completely unmanned though – a surprising 2,700 members of staff are tucked away in backroom offices or attending to the demands of the high-tech machines, adjusting and servicing them as required.
Though four million sensors are produced daily, it’s actually quite a slow and, not surprisingly, complex process. With time-consuming steps including photolithography, ion implantation and dry etching, as well as cleaning and polishing, it can take up to six months to produce a sensor that’s ready to be shipped.
Kumamoto may have an abundance of ultra-clean water, but it also sits on a geological fault line, and on the evening of April 14 2016, for the first time in its history the island of Kyushu was hit by a magnitude-7 earthquake – and just over a day later it was hit by a second earthquake of the same power.
While the factory was still standing and everyone was safe, the plant had been left with huge structural scars, including damage to the foundations. The pristine cleanrooms had been ravaged, with FOUPs scattered across the floor and some having smashed the fragile silicone wafers, while if you looked up to the ceiling of the clean room on the sixth floor you could see daylight.
Production was halted, but Sony set its factory the task of getting up and running again in five weeks, with all the staff, from senior management down, getting involved with the clean-up.
Production restarted ahead of schedule, and the plant was back up to full capacity within three months. Should the unthinkable happen again, steps are in place to make sure the recovery is even quicker.
As you can imagine, the Kumamoto earthquake had a huge impact on the global camera industry, with sensors destined for millions of cameras lying shattered on the floors of the clean rooms, not just at Sony’s plant but at neighbouring factories too. While global camera stocks ran low for a period the crisis was relatively short-lived – a testament to the determination of the staff at Sony's Kumamoto Technology Center.
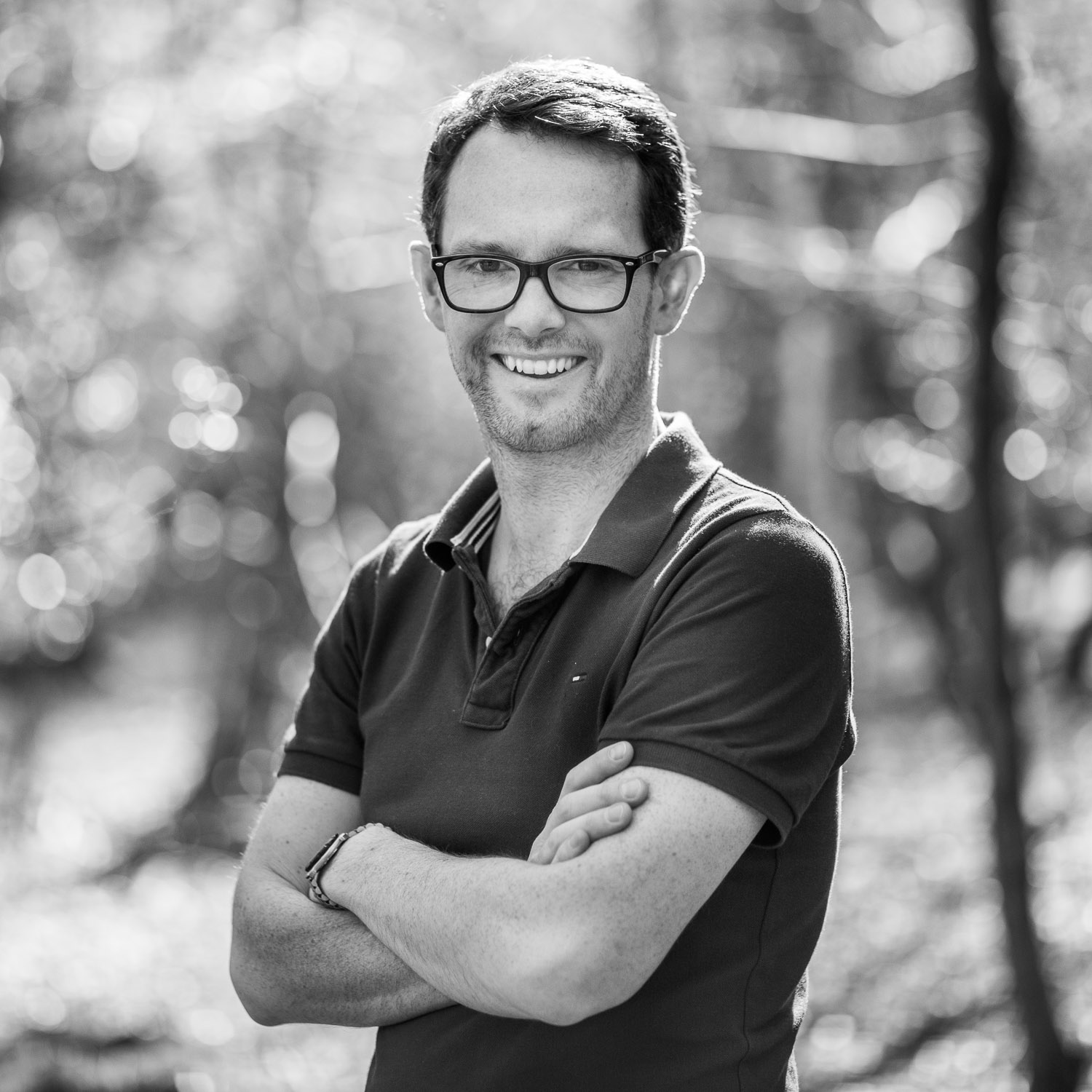
Phil Hall is an experienced writer and editor having worked on some of the largest photography magazines in the UK, and now edit the photography channel of TechRadar, the UK's biggest tech website and one of the largest in the world. He has also worked on numerous commercial projects, including working with manufacturers like Nikon and Fujifilm on bespoke printed and online camera guides, as well as writing technique blogs and copy for the John Lewis Technology guide.