Why there's never been a better time for Mac design
We take an in-depth look at the Mac's recent breakthroughs, and find out what they mean for you
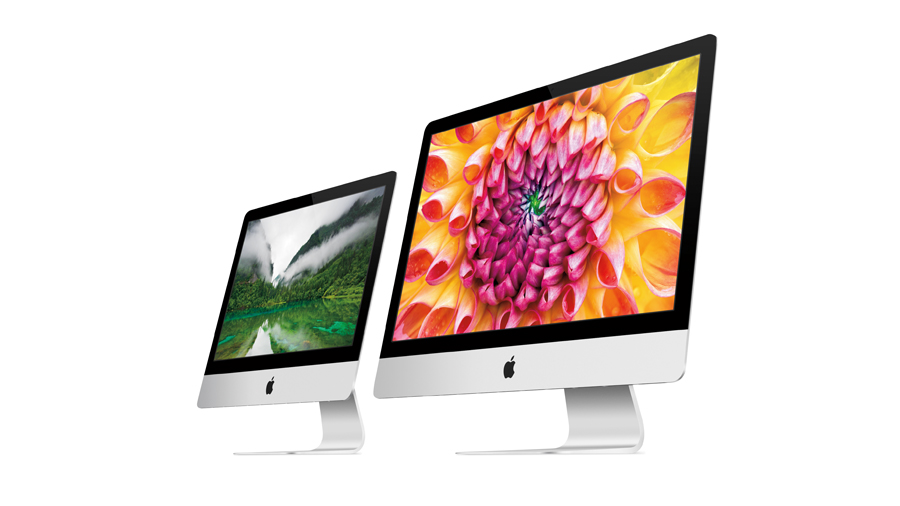
Apple has been very busy over the last few months, with new technologies taking the Mac to even greater heights.
The last MacBook Pro refresh brought us the much-vaunted Retina display, the world's highest-resolution notebook screen.
Then we got a radically redesigned iMac packed with new features, an exciting new storage solution and a 13-inch version of the Retina display MacBook Pro.
The late 2012 iMac's call-out feature is its ultra-thin case. At its edges, its body is now just 5mm thick, and it's 40% smaller in volume than the previous generation. But to achieve this thinner, smaller form factor, Apple had to raise its game in several key areas.
The first challenge faced by Apple's engineers was how to fix the front of the iMac to the rear section. Standard welding procedures such as fusion arc welding are impossible on such a thin body, so new solutions were sought.
They found one in friction-stir welding, a cutting-edge process that uses friction-generated heat and a high degree of pressure to fuse the two aluminium surfaces into a seamless joint that's incredibly strong.
Friction-stir welding is a British invention developed for use in the shipbuilding, aircraft and automotive industries. The process was also adopted by NASA for use in the now-retired Space Shuttle programme.
Sign up for breaking news, reviews, opinion, top tech deals, and more.
It works by rotating a wear-resistant cylindrical tool at between 180-300rpm, depending on the thickness of the components being welded together. This tool is pressed onto the joint at a pressure of between 5,000 to 10,000 pounds per square inch, moving along it at between 3.5 to five inches per minute. A probe in the centre of the otherwise-flat rotating, high-pressure welding tool friction-heats the joint, causing the metal to soften without actually melting.
This softened material is then forced back behind the pin, where, under the pressure of the main surface of the tool, it's bonded into a very strong joint.
Welding the case joints wasn't the only challenge faced by Apple's engineers. The ultra-thin form factor also forced a rethink in how the display is put together. Unlike previous iMac models, where there was a two millimetre gap between the LCD screen and its glass cover, here the screen is pressed against the glass using a process called full lamination.
Already used on tablet devices, this is the first time the process has been attempted on such a large screen. The LCD used in the new iMac is 5mm thinner than before too. But the full lamination process does more than shave a few millimetres off the screen's thickness. By pressing the LCD directly against its cover glass, reflections are dramatically curtailed. Light can no longer bounce off the LCD screen itself, or the back of the cover glass.
The anti-reflection coating used on the glass has been revised too. Eschewing the usual application methods, a process called plasma deposition has been used. This allows Apple to coat the glass with incredibly thin layers of silicon dioxide and niobium pentoxide, decreasing reflections from the front of the glass without compromising the integrity of the display's colours.
It was originally designed for much smaller transparent surfaces such as camera lenses and helmet visors, but Apple's engineers have managed to scale it up for use on the iMac's 21-inch and 27-inch screens. The result is that the new 2012 iMac's screen is 75% less reflective.
The new form factor has forced the optical drive to be dropped, so if you still need to burn to or read from CDs and DVDs, you'll have to buy an external drive. It's not the first Mac desktop machine to drop the optical drive, the Mac mini hasn't had one since July 2011 and both the MacBook Air range and Retina MacBook Pros were designed without one from their inception.