3D printer: MakerBot Replicator 2
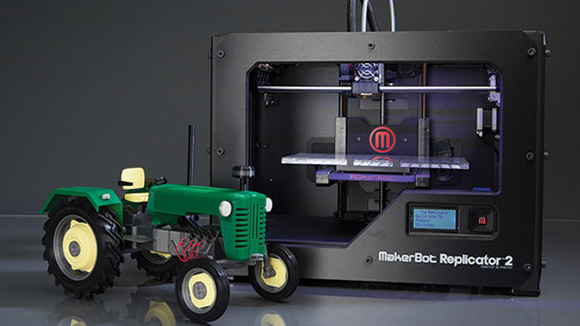
Printing your own ideas in 3D has to be the ultimate if you're into design or creating your own gear. And really, there's only one thing better than a small 3D printer sitting on your desk: a larger one.
When we tested a sub-$1,000 3D printer in the TechLife labs months ago, it was such a novelty that we had a little crowd watching that little magic box churning out all manner of 3D objects.
But as good as the UP Mini is, it doesn't take you long before you start dreaming up ideas that won't fit in a smaller printer.
So when we had the chance to take a look at the bigger Replicator 2 from 3D printer maker MakerBot, we were almost tripping over ourselves to get it out of the box.
UP Mini vs MakerBot Replicator 2
With the UP Mini as our reference point, we quickly realised just how different a beast the fast-selling the MakerBot Replicator 2 is. And it starts right from the material (filament) you make your objects from.
Whereas the UP Mini uses ABS plastic (the stuff most of your gadgets are made from), the Replicator 2 runs on polylactic acid (PLA), a type of polyester that looks a bit like fishing line. And the two have very different heating and cooling characteristics.
ABS plastic needs to be cooled slowly and maintain a temperature of 55°C while you're building your object to get best results. Otherwise, it'll curl and warp, especially when building larger objects.
Sign up for breaking news, reviews, opinion, top tech deals, and more.
It's the reason why good ABS 3D printers will have an enclosed chassis plus a heated build table (the UP Mini has both, which makes it an excellent printer for its $995 price).
PLA, on the other hand, doesn't have that issue — it cools rapidly, but doesn't warp or curl (at least nowhere near to the same degree).
As a result, you can have an open box-style printer like the Replicator 2 and not have to worry about airflow as you would with ABS.
PLA isn't perfect, though — it's less heat-resistant than ABS and is more moisture-absorbent as well.
Pulling it apart
Having that open chassis makes it even more fun to watch because you can clearly see the molten PLA plastic flowing out of the extruder head and building up your creation one layer at a time. And it's just so hypnotic to watch.
Having seen the UP Mini work, I thought I might've been over it watching the Replicator 2, but there I was, sitting in our labs, glued to this printer as if I was watching television for the first time.
The Replicator 2 comes fully prebuilt, so in theory all you have to do is level the build table (an easy, no-tools-required process), load up the bundled filament spool on the back and you're good to go.
It comes with a set of Allen keys and with good reason — 3D printers are still very new and while some huge advances have been made in the last 12 months, they still require maintenance.
If you're expecting the simplicity of an inkjet printer, remember that inkjets have had 20 years to get where they are now.
It was while watching that we spotted a problem with the filament not coming through the extruder. With phone help from the Australian distributor Bilby CNC, we pulled the Replicator 2 print head apart.
While doing this with an inkjet printer would frighten most right- minded people, the Replicator 2 is a sneakily simple design. The whole extruder head mechanism is bolted together with four long screws: two that go in from the front and two from the left side.
What's more, you only need to remove the two at the front to pull apart the main workings.