Inside the Loewe TV dream factory
Not only is Loewe a founding member of IFA (Berlin's tech extravaganza and one of the oldest industrial exhibitions in Germany) but it actually created the world's first cathode-based TV way back in 1931.
PACK IT IN: Workers pulled 10 hour days after this year's IFA
And the list of firsts doesn't end there: the first home entertainment centre was developed by the company in 1938, consisting of a TV and integrated record player; it was the first to come to market with the portable television (25cm in size with built in radio!); Loewe launched the concept of 100Hz TVs way back in 1994; and if you think the latest batch of web-enabled TVs are cutting-edge, then think again as Loewe launched its version, the Loewe Xelos @ media, back in 1997.
But the today's Loewe has changed tack somewhat. Instead of chasing headlines with claims of 'world's firsts' the company has stripped back, with its focus now on creating the best possible products within its sector, with more of a focus on design.
Currently the Loewe factory makes 1,400 TV sets a day, which get packed on to 12 trucks, ready to distribute the panels to their relevant destinations.
LEADER OF THE PACK: 12 trucks a day cart off the factory's output
The current crop of TVs are created 98 per cent by machines, with workers adding in the finer details like circuitry by hand.
Sign up for breaking news, reviews, opinion, top tech deals, and more.
BACK OFF: Some of the TV's circuitry is fitted by hand
The component fitters have a fiddly job with each board in the TVs containing around 3,700 components to make the displays work. Once everything is in place the circuit boards go through a massive oven for soldering, primed at 250 degrees, for three minutes.
Throughout the creation of a TV regular spot checks are made to make sure everything is working properly.
ART ATTACK: Loewe's Art TVs line up ready to be tested
These range from visual (where computers match up the circuitry to see if anything is out of place) to practical, where a software programme will put the boards through the sort of rigmarole they will need to get used to in the home.
SCREEN TEST: Computer algorithms put the TVs through their paces
Once circuitry is in place, the fascia and panel can be fitted. As the company doesn't make the glass themselves, they take their pick from LG, Sharp and Samsung created panels.
ON DISPLAY: The Reference screen needs two men to lift into place
In the past Loewe used to deal only with Sharp (who own a 29 per cent stake in the company) but the Korean manufacturers have upped their quality and the panels used are now chosen from those companies on a size basis.
Watching the factory team put together a TV is a fascinating process. While there's a huge amount of care and dedication to the products – even the stickers on the boxes have to be aligned in the correct way – it's all done with such ease and speed.
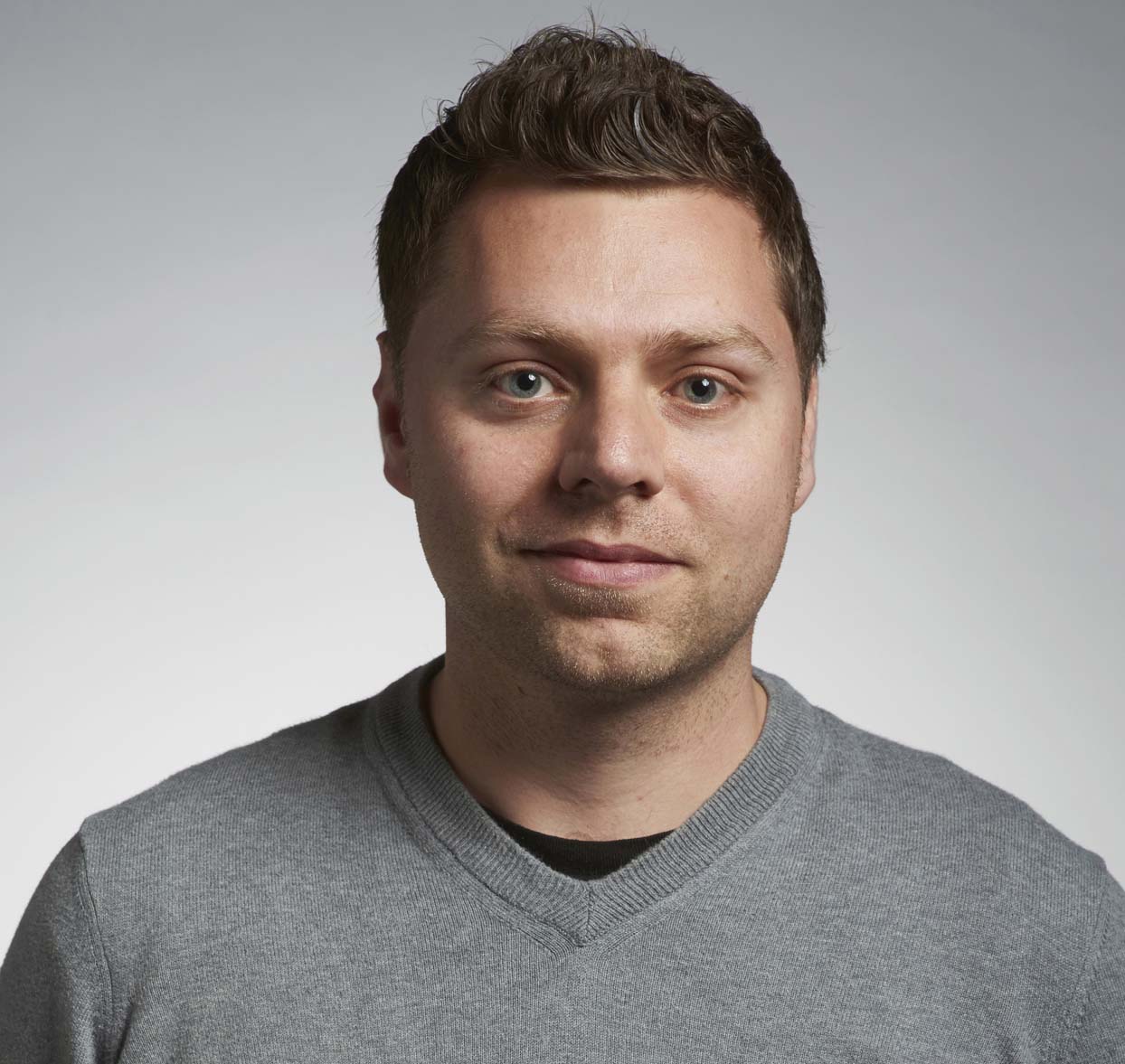
Marc Chacksfield is the Editor In Chief, Shortlist.com at DC Thomson. He started out life as a movie writer for numerous (now defunct) magazines and soon found himself online - editing a gaggle of gadget sites, including TechRadar, Digital Camera World and Tom's Guide UK. At Shortlist you'll find him mostly writing about movies and tech, so no change there then.