Love it or hate it, the Cybertruck's tech is a game changer
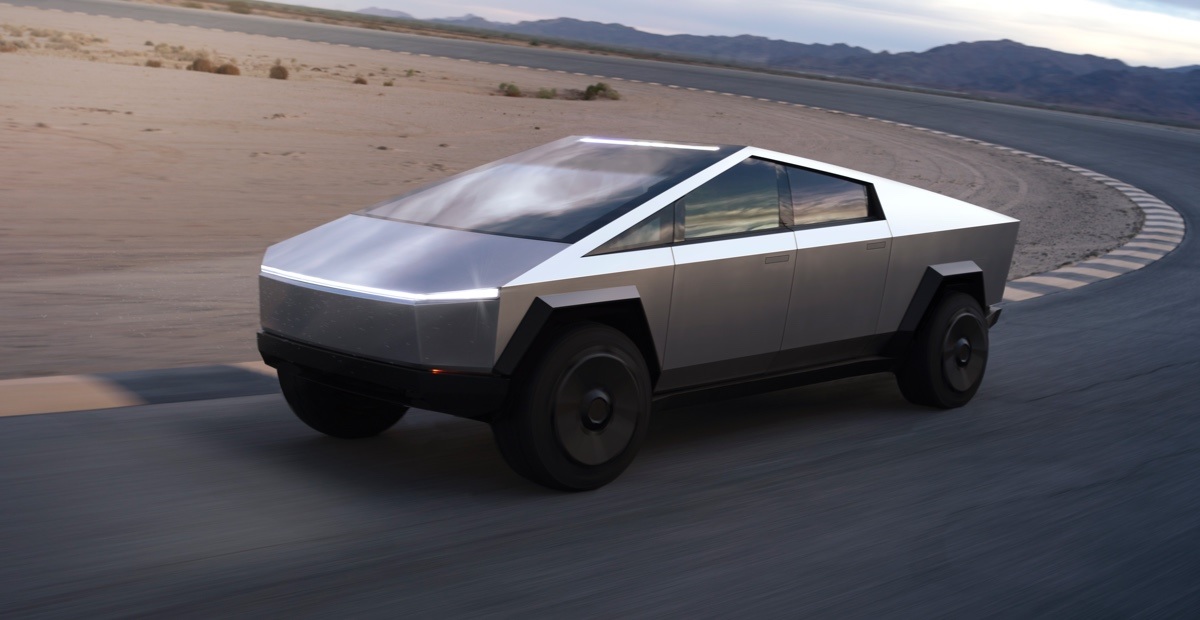
After four long years, Tesla’s Cybertruck is finally here. Deliveries started on Nov 30 and are ongoing, but reactions have been somewhat negative. Pundits are disappointed because the price is higher than originally announced, and the range is lower than initially advertised – forgetting realities like inflation and battery tech limitations. Meanwhile, naysayers are celebrating, saying, "We told you so!”
There’s no doubt Cybertruck’s design is polarizing, and I’m sure it will continue to be praised and panned alike for years to come. But what few people are talking about – and what I want to write about here today – is all the technological innovation this new EV brings to the table, and how that’s about to impact both consumers and the auto industry. Love it or hate it, the Cybertruck's tech is a game changer.
It's the first production vehicle that’s fully steer-by-wire, the first production vehicle with a 48V low-voltage system, the first Tesla with an 800V high-voltage architecture, and the first Tesla with bidirectional charging. The CyberTruck also features a radically new wiring harness, and uses some of the biggest aluminum gigacastings yet, together with cold-rolled stainless steel body panels that are structural.
Full disclosure: I’m a satisfied Tesla customer who’s owned two Model 3s since 2018, but as a tech and car journalist, I’ve also been lucky to drive almost every other EV available in the US to date. And before you think I’m just another Tesla stan, I’ve written before about why you might not want to pick a Tesla as your first EV, and why right now, there are better electric pickup options than the Cybertruck.
I don’t think the Cybertruck is pretty, but it’s certainly grown on me. A few weeks ago, I saw a prototype parked in my neighborhood in San Francisco – ironically, the same release candidate (RC) that was later towed for parking illegally – and it’s clear that in person, the Cybertruck has an undeniable presence. It’s like a sci-fi movie prop come to life, the “car of the future, future, future…” (Do you hear the echo?)
Fully steer-by-wire
Steer-by-wire isn’t anything new. It’s been used for rear-wheel steering on production cars for a few years now and is an offshoot of other drive-by-wire technologies, like throttle-by-wire (which is decades old now), and brake-by-wire, which is often used on EVs and hybrid vehicles to blend regen and friction brakes. Back in 2013, Nissan’s Infiniti Q50 was the first car to use steer-by-wire for primary steering.
What makes the Cybertruck different is that it’s fully steer-by-wire. Nissan’s decade-old tech still used a mechanical shaft from the steering wheel to the steering rack as a failsafe. In normal operation, the steering wheel was disconnected from the steering rack, but any loss of power or system failure would fall back to the steering shaft. In the Cybertruck, there’s no shaft – just a steering wheel and two steering racks (front and rear).
Sign up for breaking news, reviews, opinion, top tech deals, and more.
This results in three changes. First, turning the steering wheel does nothing unless the Cybertruck is powered on. Second, the steering is speed-sensitive, and the steering wheel only rotates about 340 degrees (one turn lock-to-lock). At lower speeds, the steering is more sensitive, letting you maneuver easily (like when parking), while at higher speeds, the steering is less sensitive, making the vehicle more planted.
Turning the steering wheel does nothing unless the Cybertruck is powered on.
Finally, the steering wheel also provides force feedback from the front steering rack and automatically returns to center, just like with a traditional steering system. Paradoxically – and while I’m personally against steering yokes replacing steering wheels – this steer-by-wire setup would be well suited for a yoke since with only one turn lock-to-lock (340 degrees), you’ll never have to make hand-over-hand turns.
In fact, Lexus offers a similar steer-by-wire system on its RZ 450e battery-electric crossover – albeit with a yoke – as an option, and only in some markets. Since there’s no mechanical failsafe, the Cybertruck’s front and rear steering racks (which are identical) use dual-redundant electric motors and triple-redundant sensors, but it’s unclear how Tesla’s handling redundancy for the power source and control electronics.
And speaking of power, the Cybertruck’s steering rack motors run on 48V, just like the rest of the vehicle (more on this below). Without a steering shaft and thicker 12V wiring, Tesla’s steer-by-wire system reduces complexity, weight, and cost. According to those who have experienced it, the Cybertruck’s steer-by-wire system initially takes some getting used to but quickly becomes intuitive and easy to use.
48V low-voltage system: an industry first
Pretty much all cars and trucks today use a 12V low-voltage system to run the majority of electrical components, from engine management in ICE (internal combustion engine) vehicles to infotainment, to lights, wipers, locks, windows, seats, and more. Some cars – like mild hybrids – have an additional 48V low-voltage system to power the electric motor and other components like active suspension.
Up until the 1950’s, 6V low-voltage systems were the norm, but as cars gained more features and electrical gadgets, 12V soon became commonplace. 24V is often used in commercial vehicles, and 48V has been discussed since the 1980s, but legacy car manufacturers and suppliers have been dragging their feet for decades. The Cybertruck is the first production vehicle to ditch 12V and use a 48V low-voltage system.
Why does 48V matter? Because electrical power (W) is the product of voltage (V) and current (A), and current dictates the thickness of wires required. For example, the Cybertruck’s steer-by-wire system uses 5 horsepower of peak power or about 3700W. That’s roughly 300A of current at 12V, or 75A at 48V. 300A requires much thicker wires than 75A. More current also means more heat, and heat is wasted energy.
Tesla is starting to roll out v4 Superchargers (350kW), which can output 800V, and can refill the Cybertruck’s 123kWh battery from 15 to 85% in just 20 minutes.
Not only are thicker wires heavier (and take up more space), but thicker wires are more expensive. So by switching the Cybertruck’s low-voltage system from 12V to 48V, Tesla was able to reduce weight, streamline packaging, minimize wasted energy, and lower material costs. Basically, a 48V low-voltage system is more efficient and more affordable. And with EVs, lower weight and better efficiency translate into more range.
Plus, by using 48V, Tesla was able to remove heat sinks from various electronic modules, making them lighter and smaller. EVs typically have a 12V battery that powers the low-voltage system and switches the high-voltage battery on when the vehicle is turned on. The high-voltage battery then charges the 12V battery via a DC-to-DC converter (instead of an alternator). If this 12V battery dies, you have to jump-start it.
Since the Cybertruck uses a 48V lithium-ion battery for its low-voltage system, Tesla had to come up with a solution to jump-start it using standard 12V power, so it designed a custom converter for this purpose. Also, the sooner legacy car manufacturers and suppliers switch to 48V the sooner 48V electrical components will drop in price, so Tesla created a guide to help other manufacturers design 48V vehicles.
800V high-voltage architecture with a neat trick
In addition to the familiar 12V low-voltage system (48V on the Cybertruck) that runs the majority of electrical components, EVs also have a high-voltage system for propulsion, which includes a massive high-voltage battery, one or more motors, and one or more inverters to control each motor (and manage regenerative braking). Today, most EVs – including all Teslas before the Cybertruck – use a 400V high-voltage architecture.
A few EVs use an 800V architecture, including the Porsche Taycan, Audi e-tron GT, Hyundai IONIQ 5 and 6, Kia EV6 and EV9, and Genesis GV60 – plus a handful of Chinese cars. The benefits of using 800V for the high-voltage system are similar to the benefits of using 48V for the low-voltage system. 800V lets manufacturers use thinner wires, which saves weight and cost, reduces heat, and improves efficiency.
The Cybertruck also benefits from an 800V high-voltage architecture. But right now, Tesla’s vast Supercharger network consists primarily of v3 (and older) Superchargers, which only support 400V. To solve this problem, the Cybertruck’s 800V battery pack is split into two 400V halves, allowing it to charge at 400V Superchargers by simply connecting the two halves in parallel using an electronic switch. Neat trick.
This approach is similar to what most Chinese smartphone manufacturers (like OnePlus, Oppo, and Xiaomi) are doing with fast charging. Any modern smartphone charging at 80W or more typically features two battery cells that are being charged in parallel. Tesla is starting to roll out v4 Superchargers (350kW), which can output 800V, and can refill the Cybertruck’s 123kWh battery from 15 to 85% in just 20 minutes.
The Cybertruck also introduces Tesla’s Powershare bidirectional charging, It’s similar to Ford Pro Power Onboard and Ford Intelligent Backup Power, which are available on the F-150 Lightning. This lets the Cybertruck share up to 9.6kW of power via two 120V outlets in the cabin, and one 240V socket plus two 120V outlets in the bed. You can also direct 11.5kW of backup power to your home through a Tesla Powerwall.
Etherloop: a radical new wiring harness
Over the past three decades, cars have rapidly gained more features, electronics, and tech. As a result. wiring harnesses have become incredibly complex and dense. The introduction of the controller area network (CAN bus) in the 1990s helped simplify vehicle wiring, but this old tech is simply no match for modern features like ADAS (advanced driver assistance systems) and multi-display infotainment systems.
Today, many cars use multiple, separate CAN buses for various subsystems, along with a smattering of automotive Ethernet. It’s a mess, and more importantly, wiring harnesses have become heavy – like 150lbs (68kg) heavy – expensive, and labor-intensive to manufacture and install. Since SDVs (software-defined vehicles) use fewer hardware components, Tesla’s always managed to keep its wiring manageable.
Cybertruck cranks things up a notch, with a radically new wiring harness that Tesla calls Etherloop. This consists of a single continuous gigabit Ethernet cable that loops around the interior of the Cybertruck.
But the Cybertruck cranks things up a notch, with a radically new wiring harness that Tesla calls Etherloop. This consists of a single continuous gigabit Ethernet cable that loops around the interior of the Cybertruck. Remember Token Ring? It connects to 368 endpoints and reduces cross-vehicle wiring by 68%. Data is time-sliced and latency is just 0.5ms. If the loop is cut, data will travel the other way around.
What’s even more impressive is that Etherloop carries all kinds of data, including digital audio to each speaker, digital signals from several mics for in-cabin ANC (active noise canceling), and digital video from multiple cameras to the FSD (full self-driving) computer – all in real-time – while cutting the weight of communication wiring in half. The other benefit is that all the data is available to every electronic module.
Aluminum gigacastings and stainless steel body panels
I’ve written about gigacasting before, but let me jog your memory. Gigacasting is a process that allows car manufacturers to cast large parts in a single piece, instead of stamping and welding dozens of separate pieces. It streamlines production, lowers manufacturing costs, reduces weight, and increases crash safety. Tesla pioneered gigacasting and currently uses it in the front and rear structures of the Model Y and Cybertruck.
Besides using some of the largest aluminum gigacastings to date, the Cybertruck also features cold-rolled stainless steel body panels that are structural. While it took some time for Tesla to perfect these manufacturing techniques, there are significant benefits. For example, since the door skins now act as structural members, traditional steel beams are no longer required inside the doors to ace side-impact crash tests, saving weight.
My takeaway
Whether you love or hate Tesla – and especially Elon’s questionable antics – there’s absolutely no denying that the company’s clean sheet approach, which isn’t constrained by the past, makes it the industry leader when it comes to engineering and manufacturing EVs. Better yet, Tesla is dragging risk-averse legacy car manufacturers and suppliers along, kicking and screaming. That’s why the Cybertruck’s tech matters.
Plus, all this new tech won’t just benefit the auto industry. It will also benefit consumers like you and me by making EVs more efficient, affordable, and easy to use. Either way, it’s a win. So, if you’re in the market for a Cybertruck, I suggest you wait a year or two. I fully expect the Cybertruck’s price will drop significantly once production ramps up as it has with the Model Y. Until then, there are other options.
You might also like
- We used the Hyundai Ioniq 5 to charge another EV
- 15 things I wish I'd known before buying an EV
- Inside the new Porsche Macan – the Android-powered EV that's ...
- Tesla's cheapest ever EV is coming – and it could be almost half the ...
- Google Maps just got an important update for EV drivers
- Your EV fast charging is about to get massively better, and here's ...
- The next Kia Niro EV will have more space, more range and ...
- EV battery size, charge speeds and range explained
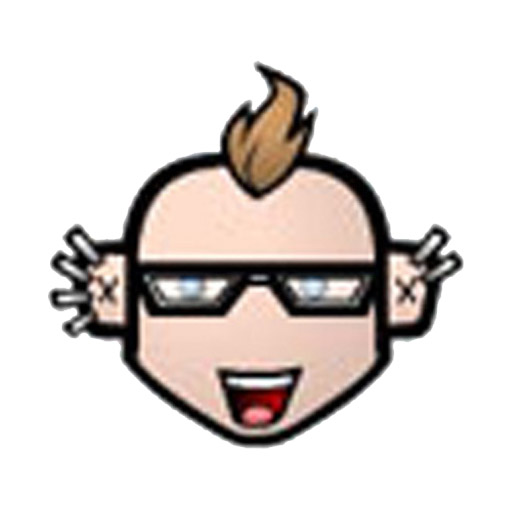
Myriam Joire (tnkgrl) was born wearing combat boots and holding a keyboard. Moments later she picked up a soldering iron. On weekends, she rally-raced with her father. She's been stomping, typing, hacking, and driving ever since. After spending years being a code-monkey in the video game industry, she joined Engadget as Senior Mobile Editor and later Pebble as Chief Evangelist. Today she hosts the weekly Mobile Tech Podcast, makes videos on YouTube, writes about tech and cars for TechRadar and other major publications, and advises startups on product/media strategy. She's based in San Francisco.