How an inkjet nozzle fires 36,000 times a second
Inside HP's secret ink manufacturing facility
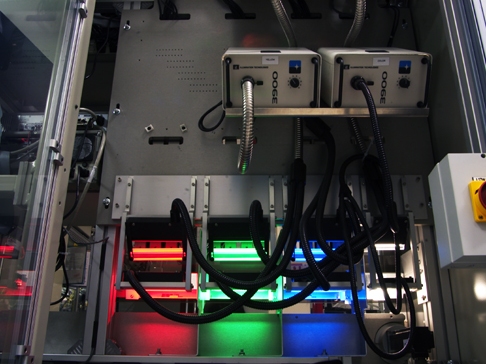
The precision needed for an inkjet nozzle to work is like dropping a grape from a 30-storey building and hitting a bucket on the pavement below. Now that's accurate. But in the case of an inkjet nozzle it's also doing it 36,000 times a second, not bad for something which is the third of a width of a human hair.
The drops fall at a speed of 50kmph – 35 million of them for every 6 x 4 photo you print.
We took the short hop over to Dublin, Ireland to check out HP's DIMO (Dublin Inkjet Manufacturing Operation) facility where it develops and manufactures ink cartridges.
Each new ink takes three to five years to develop and goes through thousands of different formulas.
"Ink is the hardest working part [of inkjet printing]," explains HP's Thom Brown. "One change or minor alteration could make a huge impact. It's wet but when you want it to be on the paper you want it to be dry," he explains.
HP came to Dublin in 1995, helped by IDA grants and has established a massive, 200-acre site. Intel's operation had already been in the area for a few years. The site is a mix of R&D and some low-level manufacturing.
How cartridges are made
Sign up for breaking news, reviews, opinion, top tech deals, and more.
At the facility we saw tri-chamber cartridges being made with integrated print heads. The early part of the manufacturing process involves putting a filter then sponge into the cartridge. It's essential that the right material is used to deliver the correct amount of ink to the nozzles – too much or not enough ink can result in the nozzles being starved or clogged.
Everything about the process is designed so no contaminants can get into the cartridge or that the different chambers inside the cartridge can't contaminate one another. The cartridges itself flies around the facility on small conveyors.
According to our guide, they can always track back if something has gone awry in the process – the cartridges all have an individual 16-digit ID laser etched on them along with a date. The lid is placed on and sealed before the cartridges are filled and everything is tested to stop leakage.
Attaching the print head is also a delicate process. Adhesive is applied on the area where the head will go, while the Tab Head Assembly (the flexible print head) is attached precisely. Any problem here and the head won't line up inside the printer. The THA is made with specifications at single-digit micron levels using a microscopic welding process.
The chip wafers are manufactured elsewhere. The so-called banner material is drilled using sand or laser in a process that creates the minute channels for ink to flow through. The material is laid across the wafer, but as it is UV curable, it needs to be kept away from UV, hence the lab we saw was bathed in yellow light. Another layer, the plating, has the holes through which the ink is actually forced and the different layers are then bonded and connected to each other.
Dan (Twitter, Google+) is TechRadar's Former Deputy Editor and is now in charge at our sister site T3.com. Covering all things computing, internet and mobile he's a seasoned regular at major tech shows such as CES, IFA and Mobile World Congress. Dan has also been a tech expert for many outlets including BBC Radio 4, 5Live and the World Service, The Sun and ITV News.