The tech of photo paper: how it's made
A closer look at what goes into producing printing material
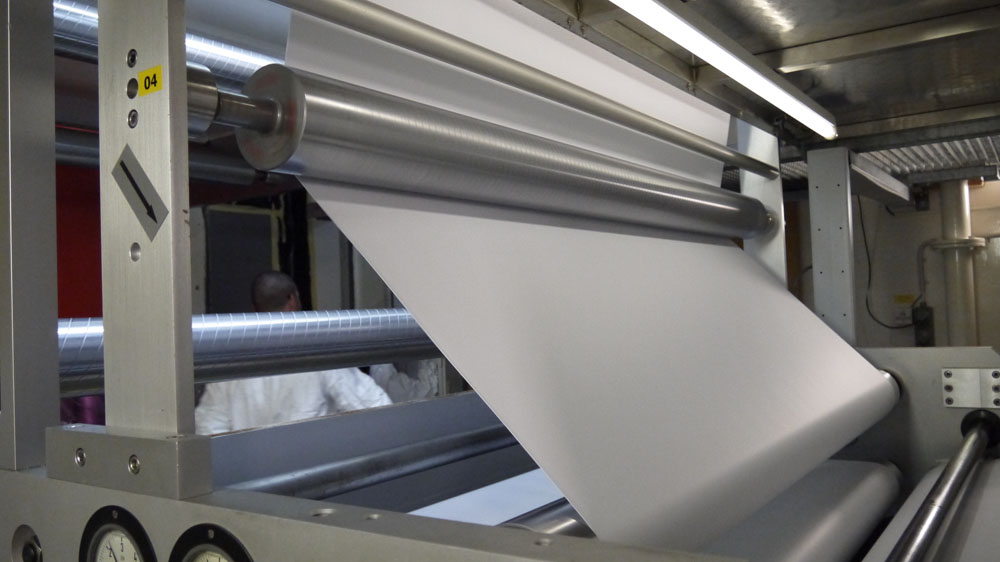
We paid a visit to the Ilford paper factory in Switzerland to take a look at what goes into producing photo paper.
Ilford is the largest independent inkjet media manufacturer in the world, and is capable of making photo paper that is compatible with almost any printer and ink combination.
- Read our Best printer 2012: 16 top inkjet and laser printers feature
The factory itself is large, and interestingly, it is not here that the paper itself is made – only its surface coatings, which transforms it from standard paper into photo quality paper, using " Ilford layer designs".
It is in this technology that Ilford believes its expertise lies, with 14% of its entire workforce (many of whom hold doctorates from various leading universities) dedicated to research and development.
Ilford is also one of the world's oldest photographic companies, having started its work in silver halide photography back in 1879.
Today, the company works with multi-layer designs, structured surfaces and nano-particles to produce its paper products.
The company creates a variety of different coatings for different photo paper kinds, including super glossy and matt products that are produced using nanoporous, polymer and hybrid technology.
Sign up for breaking news, reviews, opinion, top tech deals, and more.
Nanoporous technology was developed by Ilford for use as a receiving layer on inkjet media – and it uses it for its best-quality inkjet media.
Because the layer is porous, it can absorb ink almost instantly, leaving the paper feeling dry to the touch immediately after printing.
By contrast, polymer inkjet receiving layers enable dye inks to penetrate into the layer to give longer lasting and more stable images. Dye inks have a wider colour gamut than pigment inks, but dye inks on polymer media take longer to dry.
Any time a new coating is manufactured, an extensive testing regime starting with less than a square metre of paper all the way up to 5,000 square metres is carried out. During this testing phase, even more science and technology is implemented. For instance, infrared lasers and fine resolution cameras are used to inspect the surface for defects of every piece of photo paper manufactured at Ilford.
Much of the science and technology involved in paper production is naturally kept under wraps, but it's interesting to note that the technology can also be used in other applications.
These include agriculture, medicine, cosmetics, security systems, packaging, lighting, energy (coating for batteries) and consumer electronics, such as displays for televisions.
Ilford also works with printer manufacturers, such as Canon, which it has supported with ICC profiles made available to coincide with the launch of the Canon Pixma Pro-1, the brand's professional A3+ (16.5 x 11.7-inch) sized printer.
Other photographic industry partnerships exist, with Sony and Leica. Ilford worked with Sony to show that prints made from images taken with its Alpha cameras were of a sufficiently high standard, while Leica was worked with during the PhotoPlus Expo in 2011.
Amy has been writing about cameras, photography and associated tech since 2009. Amy was once part of the photography testing team for Future Publishing working across TechRadar, Digital Camera, PhotoPlus, N Photo and Photography Week. For her photography, she has won awards and has been exhibited. She often partakes in unusual projects - including one intense year where she used a different camera every single day. Amy is currently the Features Editor at Amateur Photographer magazine, and in her increasingly little spare time works across a number of high-profile publications including Wired, Stuff, Digital Camera World, Expert Reviews, and just a little off-tangent, PetsRadar.