Made in Japan: Discover how lenses are created
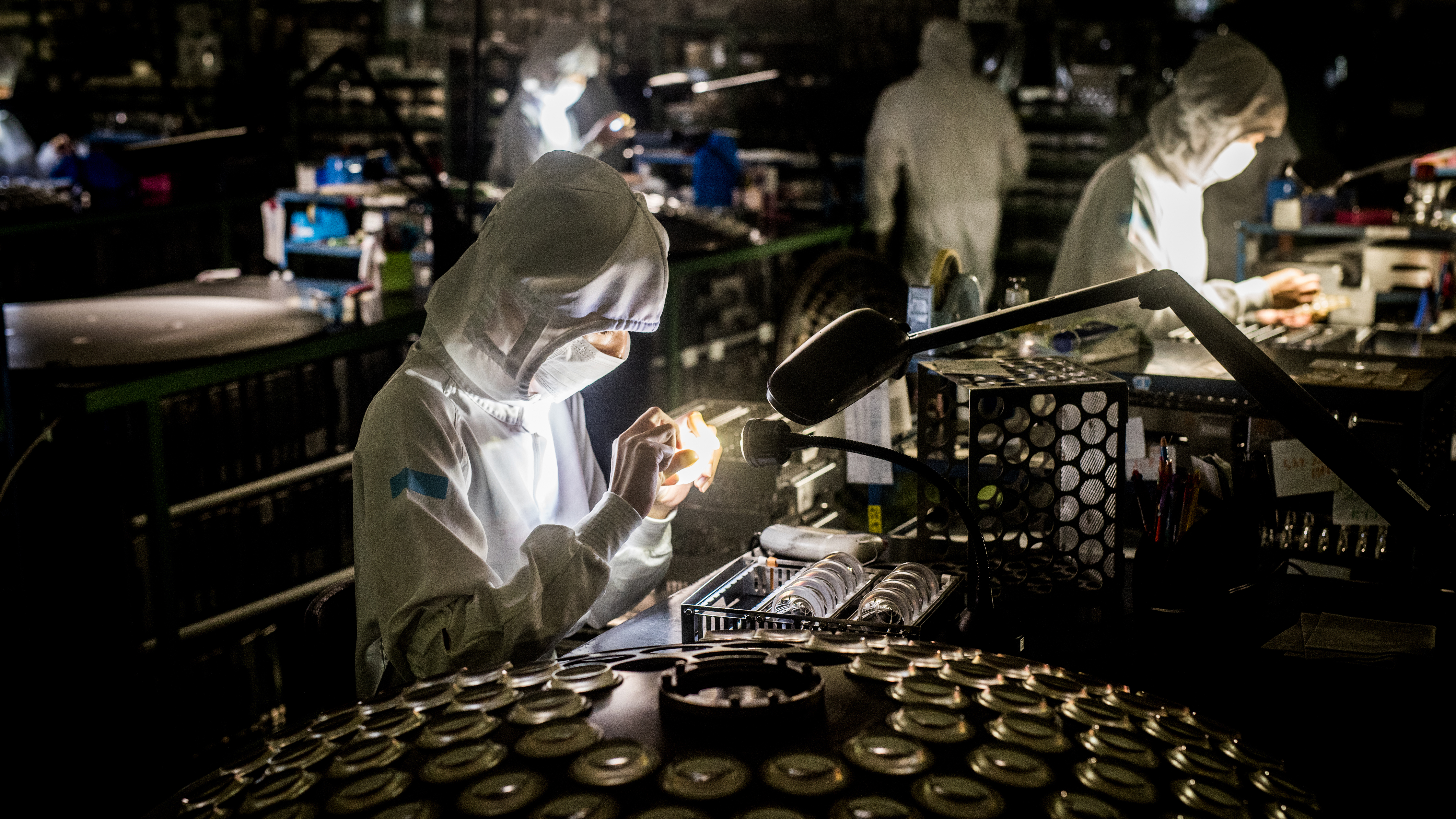
It's not every day that you get to see behind the doors of a state-of-art factory in Japan and witness first hand how a lens is made. However, we were recently invited to do just that, with a personal guided tour from Sigma CEO Kazuto Yamaki.
Mr Yamaki's father, Michihiro Yamaki, founded Sigma in 1961, and the first factory was built on in Aizu in 1974. While it's still at the same location, the site has evolved and grown considerably in the last 42 years, while Sigma's production philosophy has remained largely unchanged during that time. Sigma is committed to a vertically integrated in-house manufacturing system so it can maximise quality at the lowest cost. Local procurement is also a vital part of this model: everything is sourced in Japan.
It's no mean feat to boast a production capacity of 90,000 lenses per month, not to mention the cameras and flashguns that are also made on site. Mr Yamaki is quick to highlight the tenacious, hard-working, persistent and diligent attitude of the Aizu team's mentality as central to achieving this. So join us now on a fascinating look inside Sigma's lens factory...
1. Research and development
75% of the 1,400-strong workforce at the Aizu factory are engineers. The vertically integrated complex works to the philosophy of 'small office, big factory'. All aspects of lens, camera and accessory design and construction are tightly controlled by Sigma.
2. Machining and metal parts
The scale of this part of the factory is breathtaking. Here all the metal parts are constructed, and literally everything from the smallest screw to the lens barrel is engineered on-site. Here you can also see the construction of moulds (dies) that are used to cast the plastic of the lens.
3. Glass
To make the aspherical lenses, the glass is first ground to create the curve. Then it's smoothed and polished before being rigorously tested, then coated to reduce reflections, ghosting, flare and chromatic aberrations.
4. Injection moulding
Using the metal dies (stage 2), the plastic parts of the lens are cast. Small plastic pellets are heated and injected into moulds to make all the plastic components, which include the lens hoods and many of the internal parts.
Sign up for breaking news, reviews, opinion, top tech deals, and more.
5. Pressing and plating
Some of the metal parts, such as aperture blades, are pressed out of sheet metal. The metal parts are then anodised in vast vats. The chrome plating helps protect the parts from corrosion.
6. Assembly and electronics
Here you can see the lens elements being checked before being assembled. Once the glass is in place, the electronic components are added.
7. Test and ship
Finally, after the lens has been assembled, it's sent for rigorous testing. Here you can see a massive lens testing chart being used to test a telephoto zoom (the 150-600mm f/5-6.3 DG OS HSM | S). Once approved, it's off to be boxed and shipped out to distributors across the world.
With thanks to our guides, Kazuto Yamaki and Paul Reynolds of Sigma. This feature was originally published in Digital Camera Magazine, to subscribe, click here
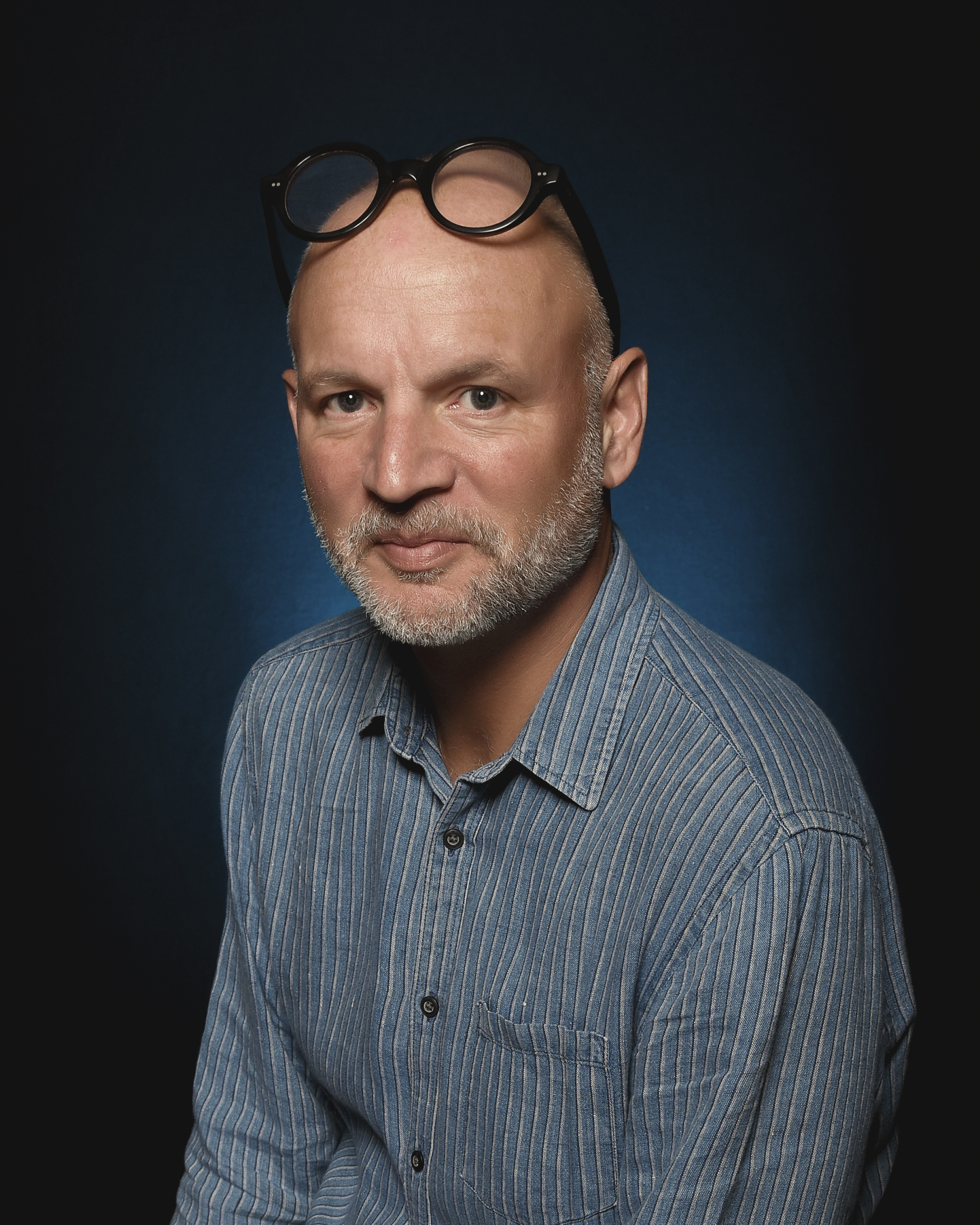
Benedict Brain is a UK-based photographer, award-winning journalist and author. He balances his personal practice with writing about photography and running photography workshops and enrichment programmes. He writes a monthly column called The Art of Seeing, and his first book, You Will Be Able To Take Great Photos By The End of This Book, was published in 2023 by Ilex Press in the UK and by Prestel in the USA with translations in Spanish, Bulgarian and German; his second book, A Camera Bag Companion, was published in March 2024. Benedict is often seen on the panels of prestigious photo competitions, and in 2020, he founded Potato Photographer of the Year. Benedict exhibits his work internationally, and travels the world as a public speaker, talking about the art and craft of photography.