How computer modelling could save your life
And save car manufacturers a lot of time
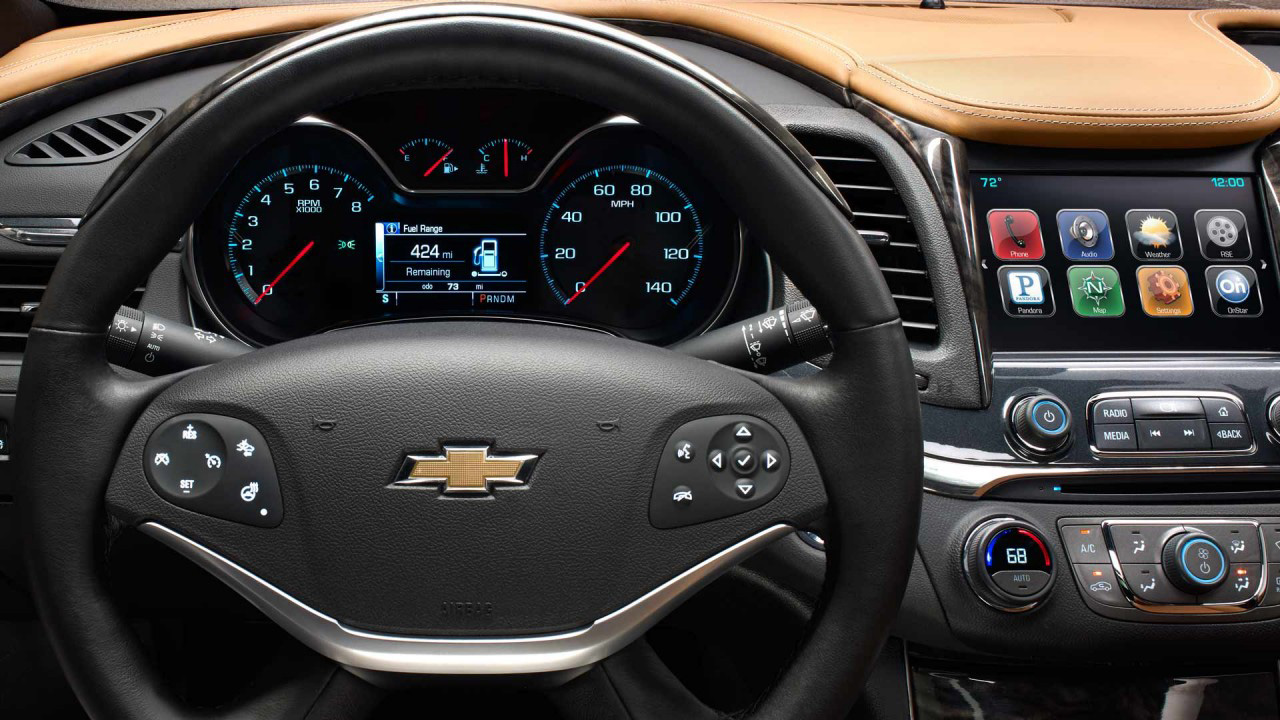
Cars have been living in a virtual world for the past few decades. Computer simulations of crash tests, stylistic changes that help us visualise a new sports car and models that analyse how much fuel you will consume on your next road trip have helped speed up the prototyping process.
Yet recent advancements in data processing, storage architectures and even a new-found faith in the merits of virtual testing have helped car makers even more.
For some, building the car of tomorrow is getting easier, and the results are safer and more reliable.
GM virtually crash tests parts in a Chevy Impala
Computer models have existed for years that show how a vehicle will deform in an accident, what will happen to the occupants, and how the airbags will deploy. In recent years, GM and other car manufacturers have created even more sophisticated models.
Mick Scherba, senior manager of global computer animated engineering strategy at General Motors, says computer crash test models are improving quickly.
"We've been able to model everyone from infant to three up to 10, 50th percentile male, from front-side-angle, rear - all of those. We've developed sophisticated occupant models that have not just the size and geometry of occupants but also the internal organs. More recently, we've worked on computer models of an occupant that flexes like a real human. As the head hits the windshield, we'd get the load imparted and look at the internal organs," he says.
The idea is to understand very specific injuries and change the vehicle accordingly. One example he gave is a model that shows what happens when the hood of a car deploys in an accident. Of course, the auto industry is moving toward lighter, stronger vehicles such as fibre-reinforced composite materials. Each material deforms differently in a model.
Sign up for breaking news, reviews, opinion, top tech deals, and more.
"If you had a hood made out of traditional steel it deforms one way, but carbon-fibre deforms another way. You've got to have a model for each," Scherba says.
Multi discipline optimisation (MDO) is the latest frontier in computer modelling for crash tests. For a vehicle like the 2014 Chevrolet Impala, GM was able to model very specific scenarios, such as a side-impact at 30mph.
But it went much further: each specific part inside the car was modelled as well, such as a rocker inner assembly or a roof-side rail. The optimisation adjusts the gauges of each part, running thousands and thousands of models.
"You end up with a vehicle that has the lightest gauges possible in all of the structural members but still meets the structural requirements for all of those load cases," says Scherba.
Amazingly, the physical tests for these individual tests would take decades to build per car for each crash test scenario. "This looks at every load-carrying part and does take several days. We run one iteration of an MDO now over several weeks," he says.
Audi models the LED lights in an R8
Lighting design is one of the most interesting advancements in car technology. With a sleek sports car such as the Audi R8, your eye is immediately drawn to a bank of LED headlights, but they also play an important role in reducing accidents - say, warning other drivers around you about a crash, emanating brighter when you brake, or casting a wide glow over the road.
Johannes Scheuchenpflug, the coordinator of simulations in the Audi department handling light functions and innovations in Germany, says the Audi engineering team works closely with their design teams to run simulations of lights in new vehicles.
"We use CAD software such as Catia V5, and software to calculate and visualise optical surfaces, such as Optis Speos and Brandenburg LucidShape," he says. Interestingly, the models - run on a cluster of computers and graphics cards - must analyse everything from wind direction and velocity to how the parts inside the headlamp will deform in a crash.
John Brandon has covered gadgets and cars for the past 12 years having published over 12,000 articles and tested nearly 8,000 products. He's nothing if not prolific. Before starting his writing career, he led an Information Design practice at a large consumer electronics retailer in the US. His hobbies include deep sea exploration, complaining about the weather, and engineering a vast multiverse conspiracy.