3D printing could benefit hugely from recycled plastics
An innovative new project aims to produce standardized filament
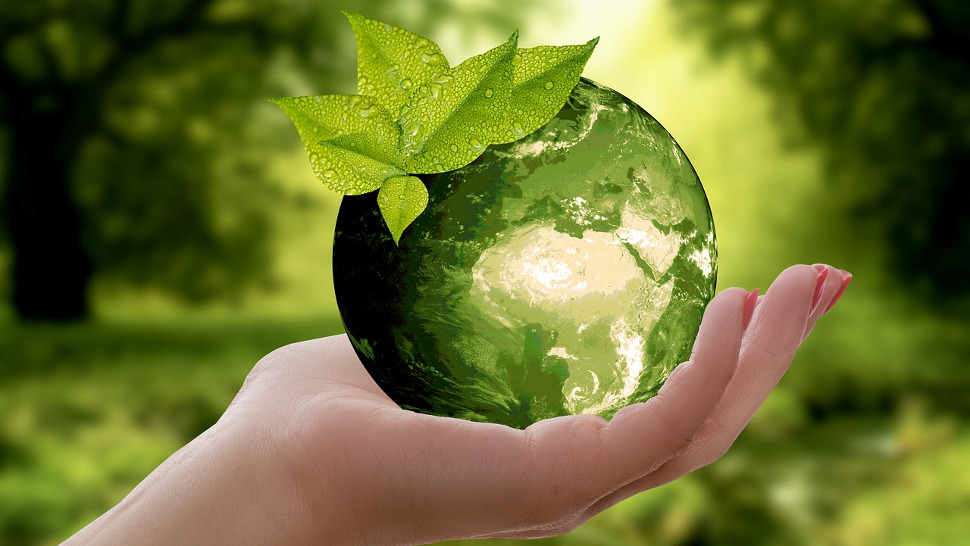
A new vision for the future of 3D printing involves standardizing filament to give users a guaranteed consistent level of quality, and using recycled plastic waste to create that filament.
This scheme comes from Aarhus University in Denmark, specifically the department of engineering, and associate professor Mogens Hinge (of the plastics and polymer engineering arm) – in collaboration with plastic processing and recycling firm Aage Vestergaard Larsen A/S.
- This is the world’s largest 3D-printed house
- Check out the best printers for home use
- These are the best 3D printers of 2020
It’s a project which has already been funded to the tune of €84,000 (around $93,000, £72,000), and Gitte Buk Larsen, marketing manager at Aage Vestergaard Larsen A/S told 3D Printing Industry: “If the project is successful, it’ll revolutionize the material consumption of 3D printers. We’re talking about being able to use plastic waste to create new, high-quality filament. It’ll have a significant impact for the environment and the climate in the long-term.”
Which has got to be good news, of course – current filament is made from new plastics as opposed to recycled.
Mogens Hinge further observes that the current state of filament in the 3D printing industry is that it’s like an unregulated ‘Wild West’ in terms of the quality you might get from any given batch.
This isn’t just about cheap or unknown-brand filament, either, but even reputable firms can see variations within the quality of their filament, from one production run to the next.
Hinge asserts: “Even if you buy a reputable-brand filament, there are still problems because there are no standards for what you put into the machine that makes the filament. This is annoying for the individual consumer, but can be disastrous for the industry, which, to a large extent demands documentation for the product.”
Sign up to the TechRadar Pro newsletter to get all the top news, opinion, features and guidance your business needs to succeed!
Printing problems
These variations in exact composition can mean that even when using the same brand and type of filament, you may not get consistent printing results with your machine’s settings, and you may be forced to adjust the temperature, feeding rate and so forth to get the right quality.
Hinge believes all the necessary details should be supplied with filament, so you know exactly what you’re working with, including the filament glass transition temperature, melting temperature, rheological properties along with surface/wetting properties.
This would go a long way, particularly in the commercial world, to ensuring that 3D-printed parts are made to a higher and more consistent standard (again theoretically cutting back on waste in that respect, too).
The eventual goal of the university’s project is to produce a standardized, fully documented filament which is, naturally enough, of a high quality and stable, and as mentioned is made from recycled plastic.
If the project comes up trumps, then hopefully we’ll see other efforts along similar lines to boot.
Darren is a freelancer writing news and features for TechRadar (and occasionally T3) across a broad range of computing topics including CPUs, GPUs, various other hardware, VPNs, antivirus and more. He has written about tech for the best part of three decades, and writes books in his spare time (his debut novel - 'I Know What You Did Last Supper' - was published by Hachette UK in 2013).