Mitsubishi zaps glass with lasers
More holes than Blackburn, Lancashire
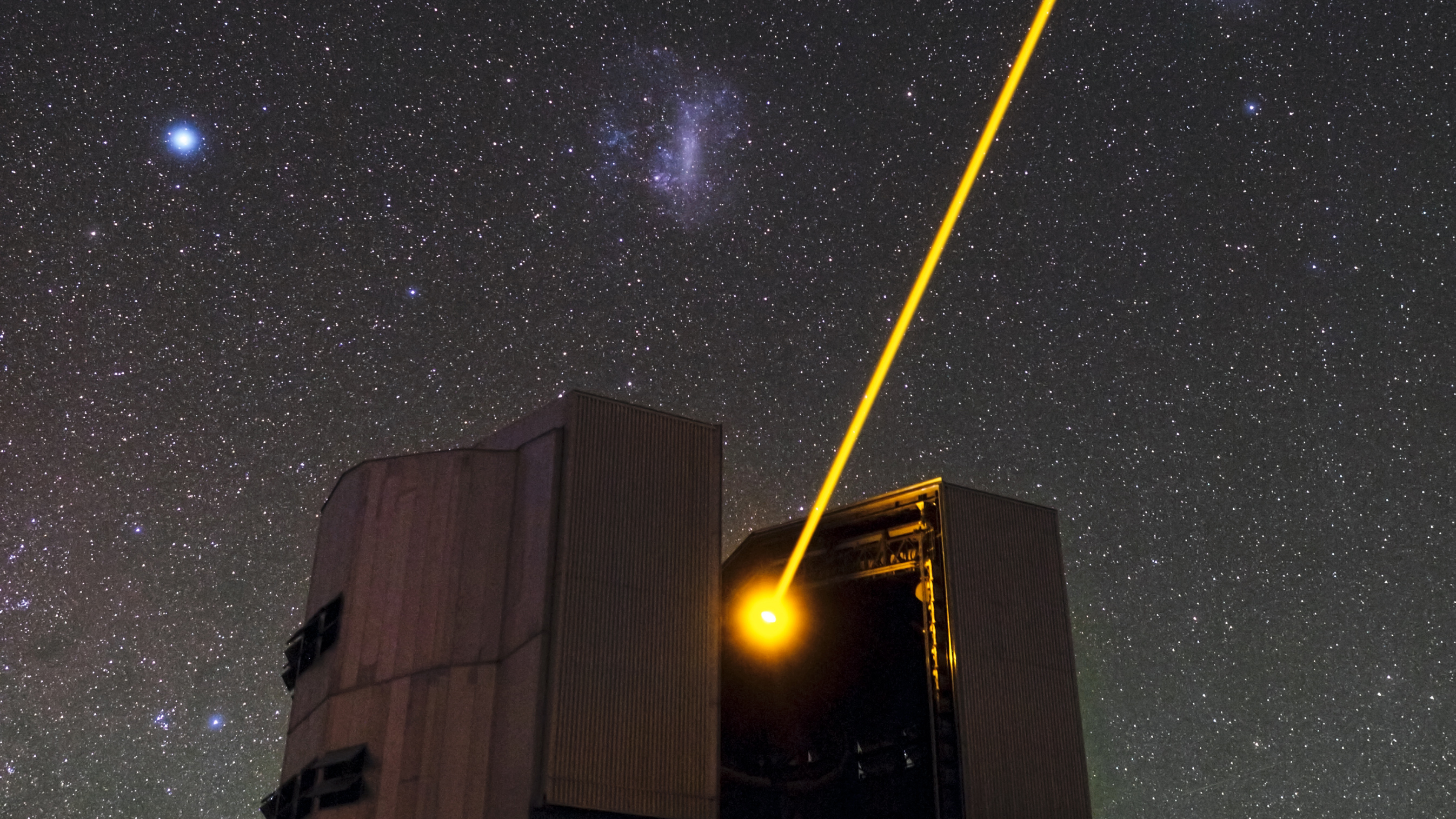
Mitsubishi Electric has developed a micro glass-processing technology that uses a pulsed CO2 laser to drill the world's smallest holes measuring just 25 microns in diameter.
This micro-drill is a key to improving glass circuit substrates for the improved performance of electronic devices.
The system uses a far-infrared CO2 laser with a wavelength of about 10 microns is used to drill transparent glass. It blasts it with short laser pulses lasting 1/1,000,000th of a second which reduces heating of the glass substrate during the drilling.
200 holes a second
More than 200 holes per second can be drilled using a high precision, high-speed galvano mirror to scan the laser beam.
Mitsubishi tells us that the CO2 lasers can easily be geared to higher power and are more efficient than conventional ultraviolet laser oscillators.
Since more circuitry is being placed into electronic glass screens this could be a way to place more detailed circuitry onto a glass surface with a higher degree of accuracy.
A spokesperson for Mitsubishi Electric told TechRadar Pro, "We think that the implementation of low cost glass interposers will cotribute to improve the performances for wide variety of electronic devices."
Sign up to the TechRadar Pro newsletter to get all the top news, opinion, features and guidance your business needs to succeed!
Ha added "Nowadays IC chips are mounted on an interposer to realize system in a package. The interposer is mounted on a printed circuit board. The main purposes of using interposer are: absorbing difference of coefficients of thermal expansion between IC chips and printed circuit board and connecting IC chips for denser and smaller electronic devices (system in a package). A glass interposer has some advantages such as low cost. But, so far, it is difficult to make a small via hole to connect chips and printed circuit board. Smaller via hole makes denser chip integration to realize a smaller electronic device. Our new CO2 laser realized the world smallest via hole and good manufacturing speed, 200 holes per min."
- Now find out why lasers are the future of our cinemas