A look at the role of the ARM Cortex-R5 in Automotive MCU Design
Future-proofing the car of today
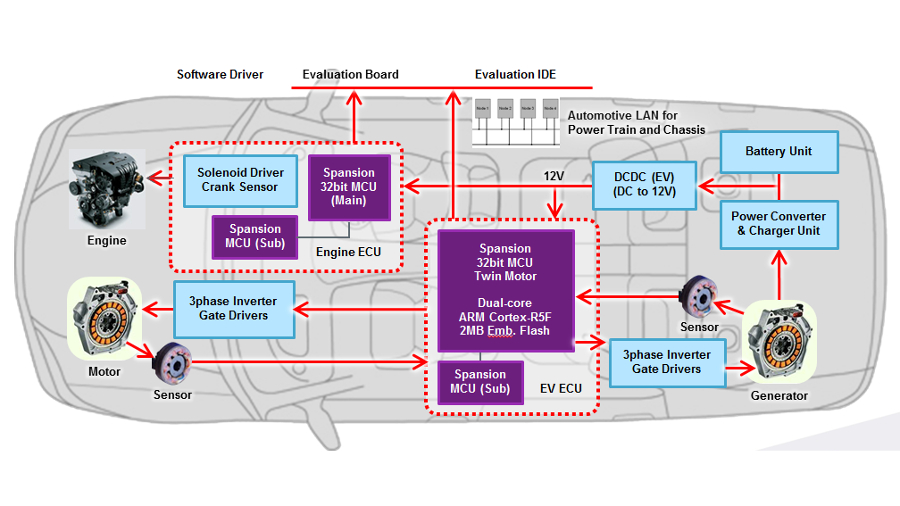
Automotive technology is undergoing a transformation, with major innovations arriving every day, including new safety systems, increased connectivity and expanded availability of telematics services.
Reliability and performance are non-negotiable for consumers – be it for the current cars on the road, or the coming wave of connected vehicles. Safety-critical applications will need to communicate via open interfaces, especially advanced driver assistance systems (ADAS), telematics and car-to-infrastructure communications.
Real-time responsiveness becomes mandatory for all automotive systems and the designs of automotive platforms need to be scalable. Therefore, future-proofing the car today is more about integrating hardware and software than innovation in mechanics.
ARM solution
This is where the ARM Cortex-R5 processor comes in, as it provides a high performance solution for real-time applications in a variety of markets including automotive. From a high-level perspective, ARM's Cortex-R series processors offer much higher performance than the Cortex-M series, while the Cortex-A series is intended for user-facing applications with complex software operating systems.
As a result, the Cortex-R5 processor is specifically intended for implementation in advanced silicon processes, emphasising improved energy efficiency, real-time responsiveness and ease of system design.
The processor provides a highly flexible and efficient two-cycle local memory interface, enabling SoC designers to minimise system cost and energy consumption. These system-level features include a high priority low-latency peripheral port (LLPP) for fast peripheral reads and writes, and an accelerator coherency port (ACP) for greater efficiency and more reliable cache coherency with an external data source.
The Cortex-R series was designed in cooperation with automotive partners and satisfies automotive requirements like real-time response, reliability and high-end performance.
Sign up to the TechRadar Pro newsletter to get all the top news, opinion, features and guidance your business needs to succeed!
High performance
Designing the embedded systems found in automotive devices is not a simple project. It requires sophisticated performance capabilities that can deliver high levels of quality, security and reliability.
The Cortex-R series processor provides fast processing combined with a high clock frequency and a deeply pipelined microarchitecture. The system comes with dual-core multi-processing configurations and hardware SIMD instructions for very high performance DSP and media functions, making it easy for developers to design for high performance needs. The capabilities of the Cortex-R5 core also fit the growing need for graphics and displays, and HMIs that provide drivers with clear, fast visual access to data.
Real-time responsiveness
With the Cortex-R series, processing meets hard real-time constraints for any and all occasions as well as fast, bounded and deterministic interrupt response. In automotive and industrial environments, this function is critical and necessary. Automotive designers are constantly tasked with keeping up with changing telematics protocols. In-car technology must be responsive to surroundings and the inner workings of the vehicle, ensuring the passengers' safety.
The architecture also includes tightly coupled memories (TCM) local to the processor for fast-responding code/data and low latency interrupt mode (LLIM) to accelerate interrupt entry.
Functional safety
Functional safety is at the core of the Cortex-R processor series. The system is dependable and reliable with high error resistance, and user and privileged software operating modes with Memory Protection Unit (MPU). The processor architecture includes ECC and parity error detection/correction for Level-1 memory system and buses and dual-core lock step (DCLS) redundant core configurations.
Cost effectiveness
The processor provides a highly flexible and efficient two-cycle local memory interface, enabling SoC designers to minimise system cost and energy consumption. With best-in-class energy and die area, the technology provides cost efficient techniques to bringing automotive MCUs to market quickly.
In design, the configuration makes it possible to include or exclude features to optimise power, performance and area. Additionally, fast development and testing with configurable debug breakpoints are available, and watch points through CoreSight debug access port with embedded trace module options speeding up time to market. Customers can now design with a much simpler and cost effective interface while not giving away either performance or features.
These features make the Cortex-R5 processor a pronounced resource for automotive MCU design, enabling automotive MCU designers to deliver high performance, enhanced human-machine interfaces, high security and advanced networking protocols tailored for a broad range of automotive applications such as electrification, body electronics, battery management, automotive cluster displays, HVAC and ADAS.
MCUs that are developed with ARM Cortex-R processor can enable scalable and efficient designs of high performing and secure automotive applications that will improve drivers' safety and user experience with the latest technology advancements in cars.
Case Study: The Traveo Family of Automotive MCUs
The Spansion Traveo microcontrollers based on the ARM Cortex-R5 delivers high performance, enhanced human machine interfaces, security, and advanced networking for embedded systems.
The first product of the Spansion Traveo family, the MB9D560, features dual ARM Cortex-R5 cores with 2MB of embedded Flash and operates at 200MHz. Additionally, Spansion is the first to use the ARM Cortex-R5 with integrated resolver digital converter (RDC).
With the help of the ARM Cortex-R5, this family of microcontrollers greatly expands Spansion's MCU portfolio for hybrid electrical vehicles (HEV) and electrical vehicles (EV). The dual-core/dual-motor control structure on a single chip allows the simultaneous control of two motors, for example the motor and the generator of an electrical engine system have to function at the same time. Both motor control modules have their own embedded interface circuits for resolver sensors, and include unique hardware IP to speed up motor control operations.
The dual-core approach and several inbuilt diagnosis functions support the required level of functional safety. By integrating these functions in a single chip, OEMs can improve the performance and save costs versus previously having to use four different chips, two MCUs and two RDCs. Improving the communication between these integrated components results in significantly faster real-time system response.
- Dr. Saied Tehrani is senior vice president and chief technology officer at Spansion